Global Energy Services Alliance (GESA) is a pioneering joint venture between Pro-Per Energy Services and Baseload Power, dedicated to setting the benchmark in aeroderivative turbine services around the world. At GESA, our mission is to empower the energy sector with unparalleled expertise and innovative solutions, ensuring operational excellence and sustainable success.
GESA's foundation is built upon a highly skilled team of aeroderivative turbine specialists, proficient in mechanical, electrical, and control engineering. Our diverse team is equipped to offer comprehensive manpower support, catering to a broad spectrum of needs from technical field advisory to complete project management.
Our Experience
Our hands-on experience spans a variety of aeroderivative turbines, including but not limited to:- GE: LM2500, LM2500+, LM6000, LMS100
- Pratt & Whitney: FT4, FT8
- Siemens: A35 (RB211), A65 (Trent60), SGT400, SGT500
- MAN, THM, Solar turbines
This extensive expertise enables us to offer a full suite of services to enhance turbine performance and reliability:
Why Choose GESA?
Choosing GESA means partnering with a leader in aeroderivative turbine services, committed to delivering excellence at every project phase. Our approach is tailored to meet the dynamic needs of the energy sector, backed by a track record of success and innovation. Let GESA be your partner in driving performance and achieving sustainable growth.
Discover how our tailored solutions can enhance your operations. Contact us today to explore the possibilities with GESA, where excellence in energy services begins.Highlight Projects:
On-Site HSE Maintenance in QATAR
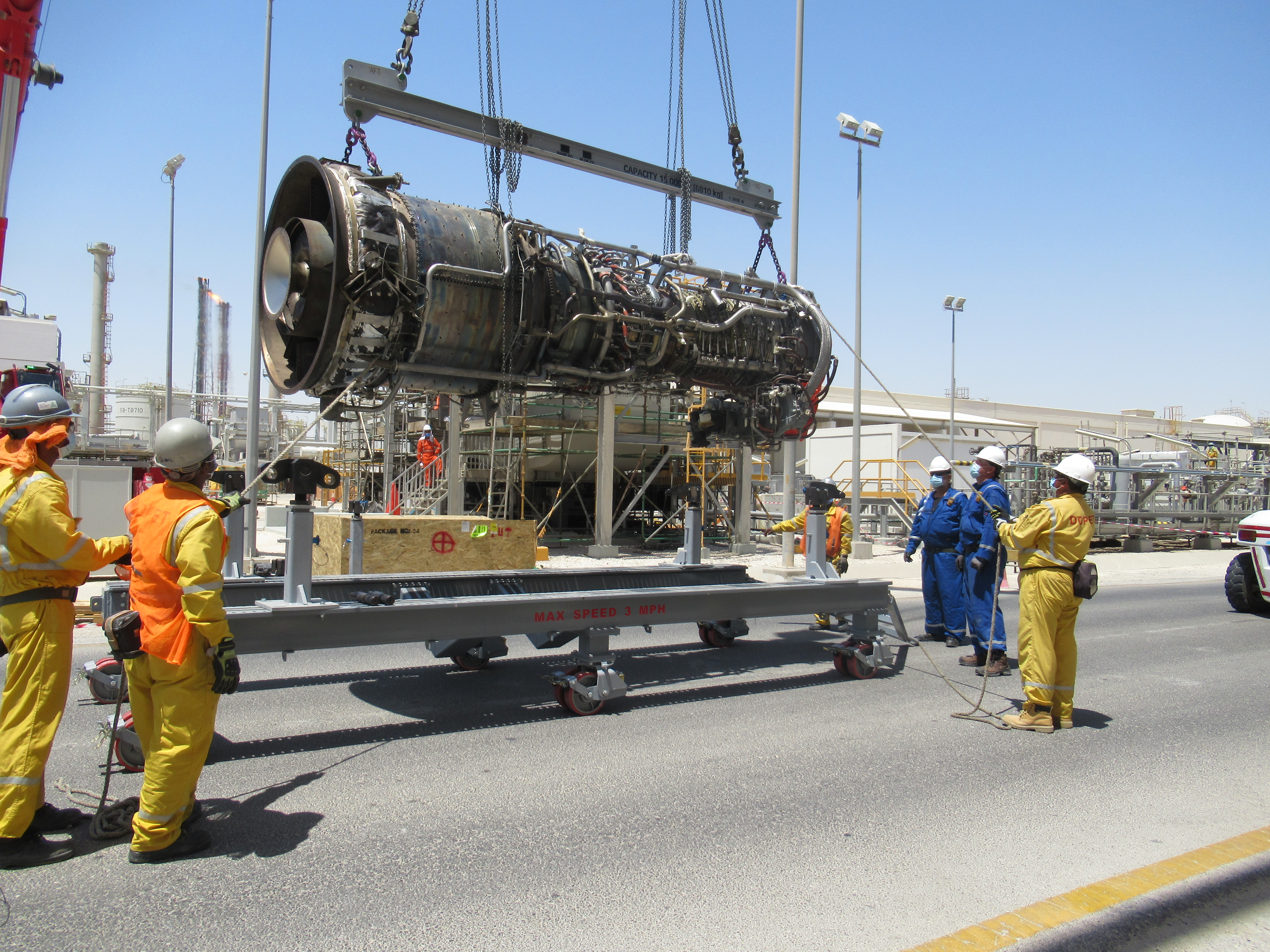
Project Scope
Performing an on-site hot section exchange (HSE) maintenance on an aeroderivative turbine is a critical task that demands meticulous planning, precision, and expertise. This process involves several key steps, each crucial for ensuring the turbine's optimal performance and longevity.
1. Preparation and Proper Tooling: The maintenance begins with the preparation of the site and ensuring that all necessary tools and equipment are available. Providing proper tooling is essential for the efficient execution of the HSE maintenance. The use of specialized, high-quality tools minimizes the risk of damage to the turbine components and ensures that the maintenance can be performed accurately and safely.
2. Provision of Original HSE Parts: Utilizing original manufacturer HSE parts is crucial for maintaining the integrity and performance of the turbine. These parts are designed to meet specific engineering standards and tolerances, ensuring compatibility and reliability. The use of original parts helps in preserving the turbine's efficiency and extends its operational life.
3. Engine Removal: The engine removal process is executed with precision and care to prevent any damage to the turbine structure or surrounding components. This step requires skilled technicians who understand the intricacies of the aeroderivative turbine's design and can navigate the complex disassembly process.
4. Professional Execution of the Maintenance: The hot section exchange is performed by experienced professionals who specialize in aeroderivative turbines. This team meticulously replaces the hot section components, ensuring that each part fits perfectly and functions as intended. Attention to detail during this phase is paramount to avoid any future operational issues.
5. Proper Reinstallation: Once the HSE maintenance is complete, the turbine engine is carefully reinstalled. This process is as critical as the removal, requiring precision to ensure that all components are correctly aligned and securely fastened. Proper reinstallation is vital for the turbine's overall performance and safety.
6. Commissioning and Start-Up: The final step involves commissioning and start-up of the turbine to ensure it operates at optimal efficiency. This phase includes rigorous testing and adjustments to calibrate the turbine according to manufacturer specifications. Successful commissioning and start-up signify that the turbine is ready to resume operation, providing reliable and efficient power generation.
Throughout this process, emphasis is placed on professionalism, the use of original HSE parts, and the application of proper tooling to ensure that the maintenance is carried out to the highest standards. The goal is to restore the turbine to its peak performance, ensuring it continues to operate efficiently and reliably for years to come.