At GESA, our goal is to harness our extensive expertise and cutting-edge solutions to enhance efficiency, reliability, and sustainability across the energy sector, with a special focus on generator systems.
GESA boasts a premier team of generator maintenance and repair specialists, holding deep-seated knowledge in mechanical, electrical, and electromechanical systems engineering. This well-rounded team is adept at providing comprehensive support, ranging from expert technical advice to full-scale project management.
Our Experience
Our experience in generator systems is both broad and diverse, spanning various models and manufacturers, including but not limited to:
- Brush
- GE
- Meiden
- Mitsubishi
- Hitachi
- Meiden
With this extensive expertise, we are well-positioned to offer a full spectrum of services aimed at boosting generator efficiency and reliability:
Why Choose GESA?
Opting for GESA for your generator maintenance and repair needs means partnering with a leader in the industry, committed to excellence in every project stage. Our customized service offerings are designed to meet the unique challenges of the energy sector, marked by a tradition of innovation and successful project delivery. With GESA, you gain a partner equipped to navigate the intricacies of generator operations, ensuring optimal performance and enduring success. Discover how our bespoke solutions can revolutionize your generator operations. Contact us to explore the opportunities with GESA, where unparalleled excellence in energy services begins.Experience the impact of our tailored solutions on your operations. Reach out today to learn more about our expertise and how we can contribute to your success with GESA, setting the benchmark for excellence in energy services.
Highlight Projects:
Major Maintenance
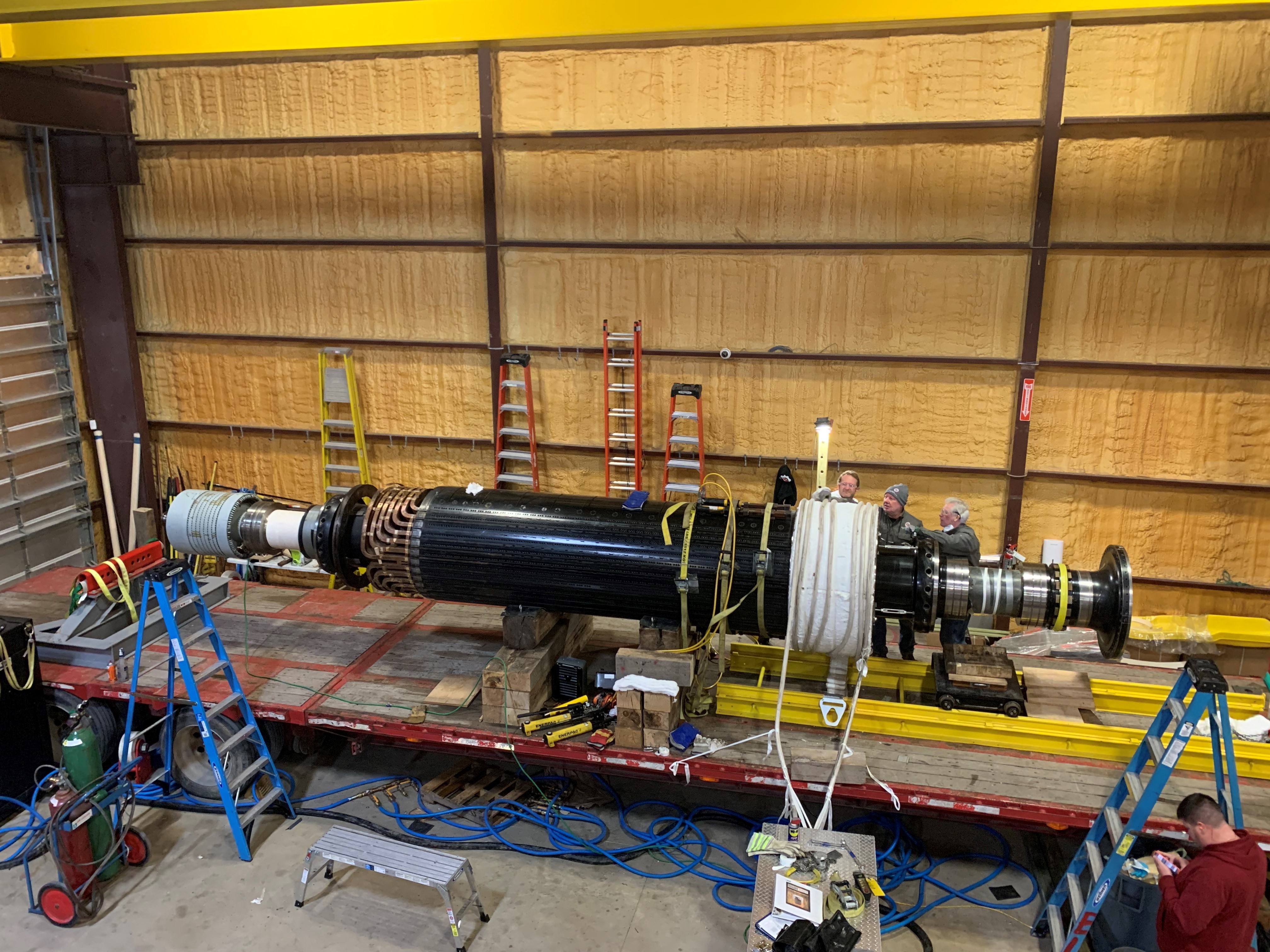
Project Scope
On-site Major Maintenance of a steam turbine is a detailed, strategically planned process designed to optimize performance and extend the turbine's operational lifespan. This comprehensive procedure encompasses several key steps, specifically tailored to address the unique requirements of steam turbines.
1- Proper Tooling: Proper Tooling: Essential to the success of Major Maintenance is the utilization of appropriate tooling. Precision tools and specialized equipment are crucial for the accurate disassembly, inspection, and reassembly of turbine components. These tools are specifically designed to accommodate the turbine's specifications, ensuring that maintenance tasks are performed safely and effectively, thereby minimizing the risk of damage to delicate turbine parts.
2. Spare Part Supply: Integral to the maintenance process is the provision of spare parts. Having a ready supply of the necessary spare parts, including OEM-approved replacements, ensures that any worn or damaged components can be promptly and efficiently replaced. This not only facilitates a smoother maintenance process but also helps in maintaining the turbine's performance and reliability by using parts that meet the original specifications.
3. On-Site Completion: TPerforming the maintenance on-site provides significant benefits, including reduced downtime and the elimination of logistical challenges associated with transporting large turbine components. Equipped with portable tooling and the necessary parts, a skilled team conducts the maintenance directly at the turbine's location. This approach allows for immediate problem-solving and adjustments, ensuring that the maintenance is completed efficiently and effectively.
4. Professional Execution: A team of professionals specializing in steam turbine maintenance carries out the maintenance process. Their expertise ensures that every aspect of the maintenance is conducted according to the highest standards of quality and safety. Through thorough inspection and servicing, the team leverages their extensive experience to identify and address any potential issues, ensuring the turbine's performance remains uncompromised.
5. Start-Up Support: Following maintenance, a careful and controlled start-up process is crucial. This includes extensive testing and calibration of the turbine's systems to ensure they operate correctly under load. The maintenance team provides vital support during this phase, monitoring the turbine's performance, making necessary adjustments, and verifying that all systems function as expected. This support is critical for a smooth transition back to full operational status, ensuring the turbine's reliability and efficiency for future operations.
In conclusion, on-site Major Maintenance of a steam turbine is a critical and intricate process that requires precise tooling, a ready supply of spare parts, the expertise of a professional team, and comprehensive start-up support. This meticulous approach ensures the turbine is maintained to the highest standards, leading to reliable and efficient operation and an extended service life.